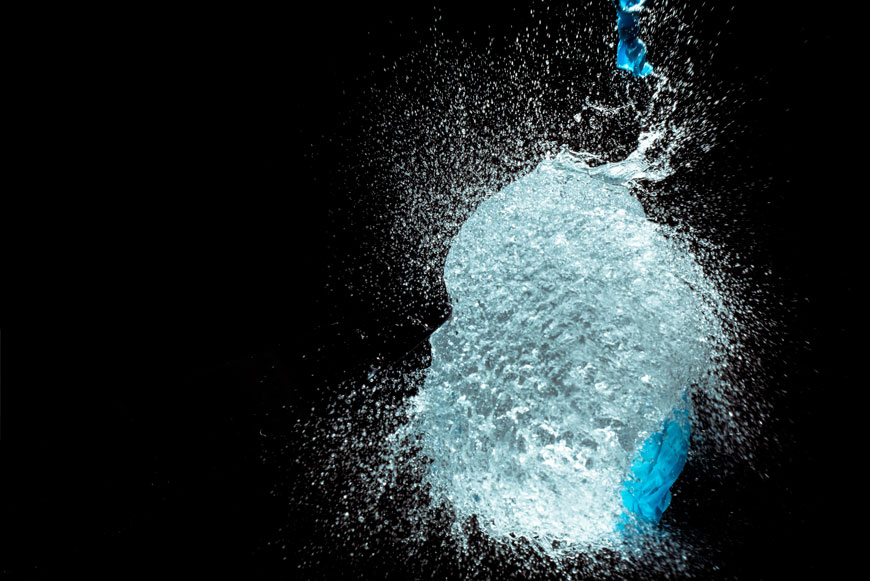
Who has ever been excited to paint something -- a bicycle frame, an old metal table, a lamp -- and then started painting the object only to realize how messy, smelly, and imperfect the whole process is? Accidentally kick the dropcloth and drip paint on your wood floor; forget to open a window and the VOCs (Volatile Organic Compounds, or compounds with a high vapor pressure at ordinary room temperature) make you feel faint; use an old brush and find it impossible to get the paint on smoothly, without brushmarks. Luckily, there is another way to paint, and a better way: powder coating. And soon, J.R.’s Maintenance will be able to provide this painting service to our customers.
Powder coating is exactly what the name suggests, a method of painting that coats surfaces with powder. It’s a method of painting, patented in the mid-20th century, that is typically used on metal surfaces, but is sometimes used on glass or other hard materials. After the powder is applied, it is then cured, which hardens the paint. In fact, one of the advantages of powder coating over traditional wet paints is how much harder powder coating is after curing. Wet paint can only get so hard, and often ends up chipping, flaking, or peeling. Powder coating, because it is not delivered by a liquid solvent and is cured at high temperatures, is very hard and does not wear down easily. It can also be applied more thickly that wet paint, which requires coat after coat to achieve thickness.
J.R.’s Maintenance is investing in powder coating equipment because we manufacture metal (including carbon steel, stainless steel, and aluminum) for our clients who have to then take the objects elsewhere for painting. With our new paint gun, tank, and curing oven, we can save our clients a trip, and our clients will know they are getting a great product. We’ve enjoyed getting acquainted with the new equipment. Let’s start with the spray gun. This powder applicator is known as an “electrostatic gun.” The powder passing through the tank and gun receives a positive electric charge, making it adhere to the grounded metal object efficiently and evenly. One great advantage of painting this way is the lack of VOCs. There are simply no fumes. The curing process then follows. To properly cure objects we paint with the electrostatic gun, we purchased a powder coating oven. When the painted object is placed in this oven, the powder undergoes a chemical change under the high heat (somewhere around 400℉) and is fused to the metal in as little as 10 minutes. And that’s it, job done. This sure beats the 30 minutes to an hour that you have to wait between coats of wet paint. With powder coating, you can apply as thick a coat as you want in one go--the object won’t need a second coat.
J.R.’s Maintenance is proud to begin offering this powder coating service to our clients. Now, if a restaurant needs a new sign, or a company needs a batch of stainless steel, carbon steel, or aluminum parts, they can put their order in with us and pick up the machined, fabricated, and painted piece from us.